TRESU flexo printing integration unit seamlessly integrates with the water-soluble pouch converting process, enabling detergent manufacturers to meet safety legislation and maintain single-pass productivity.
The European Union’s safety directive 67/548/EEC requires individual capsules used in dish washers and washing machines to carry warning messages.
TRESU has developed a printing solution, customised for integration into water-soluble detergent pouch converting lines, enabling manufacturers to meet the latest safety requirements, promote consumer protection and maintain seamless, uninterrupted single-pass production with no extra handling required. This proven technology has been developed by TRESU, in collaboration with a large global consumer goods manufacturer with plants at several locations.
This common impression flexo unit, contained within a space-saving module before the pouch-filling stage, optimises productivity by printing multiples of pouches in the cross direction. The unit prints three colours on the inside of the substrate, protecting the printed message from abrasion through the packing or logistics process.
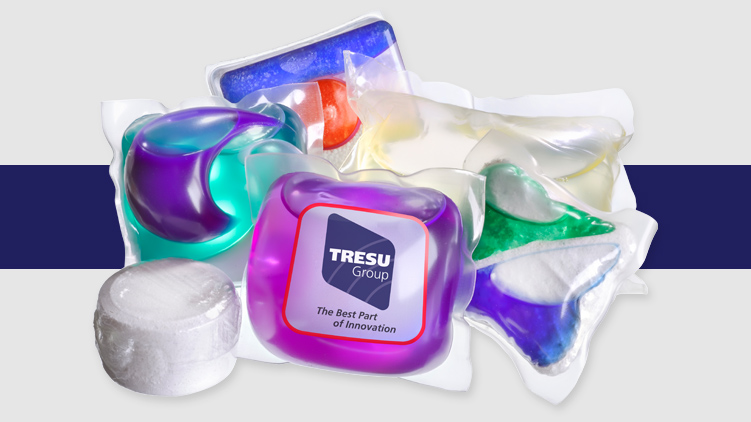
The unit has been designed with highest levels of automation. This ensures controlled, precise print speed and ink flow, at relatively low speeds, and allows easy operation without previous printing experience.
In compliance with stringent end-user requirements to assure consistent quality at several locations around the world, the machines feature identical components and procedures.
• Fully servo-driven.
• Self-regulating ink supply system.
• Customised to the speed of the pouch-filling process.
• A register module maintains precise positioning of fine text automatically throughout the production run.
• A control system stores and instantly recalls job recipes, so no re-entry of ink and calibration data is needed.
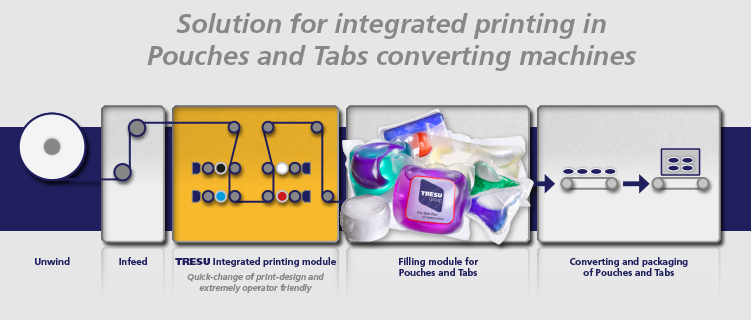
We understand that every minute counts. TRESU has optimised the system to ensure maximum uptime and fast job changes.
• A control system stores and instantly recalls job recipes, so no re-entry of ink and calibration data is needed.
• At the installation stage, the TRESU technical team works with the customer to build a unique database of recipe settings for each job, including, among others, impression settings, print levels, flow rate, air velocity, temperature and register coordinates.
TRESU’s engineers work with you from the concept stage to ensure a printing solution seamlessly suited to your unique converting needs. Moreover, we’re here to support you with training and troubleshooting, to minimise the learning curve and ensure maximum return on investment.
Relevant links:
Directive 67/548/EEC
Regulation (EC) No 1272/2008
Directive 1999/45/EEC
Read press releases and articles:
Newsroom article: Pouches and Tabs
For more information please contact:
Allan Sander
Sales Director, TRESU Solutions
Phone: +45 7632 3500
Direct Phone: +45 7632 3651
Mail: asa@tresu.dk